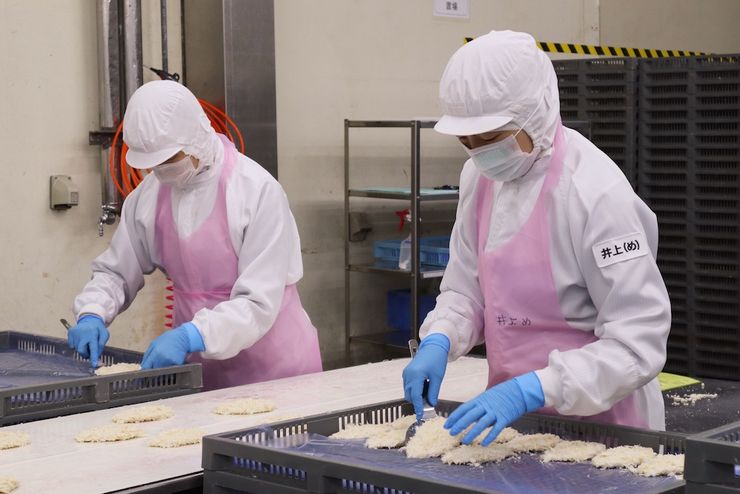
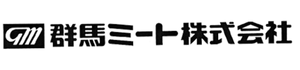
群馬ミート株式会社
- 業種
- 製造業(食品製造)
- 導入規模
- 1〜50名
- 利用目的
- HACCP
HACCP対応で複雑化した品質管理をカミナシで効率化し、75%の作業時間削減を実現
群馬県前橋市に本社を有する食肉卸・加工・販売会社「群馬ミート株式会社」は、HACCP対応に伴う業務負担の解消などを目的にカミナシを導入しました。その結果、製造部や品質管理部など、自社の幅広い領域で業務効率化を実現したほか、年間10,000枚以上の用紙削減、25,000枚以上のラベル削減などの効果が生まれています。
カミナシの導入を推進した品質管理部次長の飯嶋様に、導入前の課題や現在の活用状況、導入効果などについてお伺いしました。
課題
- HACCP対応に伴う業務負担増加の解消
- 用紙などにかかるコスト削減
- 作業記録の記入ミス・記入漏れ
群馬ミート株式会社について
70年近い歴史を持つ、老舗の食肉卸・加工・販売会社
── 群馬ミート株式会社(以下、群馬ミート)の事業概要を教えてください。
飯嶋様:群馬ミートは、1952年(昭和27年)に創業された、食肉の卸・加工・販売会社です。食肉のカットや加工をして、県内のスーパーやチェーンストアに販売するほか、飲食企業などに向けて原料肉の卸売も行っています。また、お客様のご要望を受けて、自社で冷凍フライなどのメニュー開発を手がけることもあり、適切な部位やカット方法をご提案しながら、お客様ごとに最適なメニューをお届けしています。


カミナシ導入前の課題、導入の経緯
複雑で細かいチェックシートが、製造部、品質管理部、管理職の業務負担になっていた
── カミナシ導入前の課題を教えてください。
飯嶋様:2021年6月からのHACCP完全義務化に対応するなかで、製造部や品質管理部、管理職など、複数の領域が業務負担に悩んでいました。
例えば、製造部が現場で用いるラベルの運用は、無駄な業務負担を生む原因になっていました。ラベルは商品に貼付して賞味期限などを表示するために用いているのですが、商品の出荷後は手元に残らないため、同一のラベルを複数発行して、社内で保存しています。しかし、加工工程の途中に、ラベルを確認してチェックシートに記入する記録作業が3回発生するため、商品に貼付するものとは別に、確認用のラベルを3枚も発行しなければいけませんでした。
確認のためだけにラベルを発行するのは費用の無駄ですし、ラベラーは品質管理部が管理しているため、製造部の従業員はラベルが必要になるたびに、品質管理部にラベルの発行を依頼して、受領するといった作業が必要でした。一回につき20分程度の作業ではありますが、ほぼ毎日発生するため、積み重ねによる業務負担は少なくありません。
一方で、品質管理部では、チェックシートの管理に手を焼いていました。
記入が終わったチェックシートは回収され、品質管理部が仕分けやファイリングを行います。この作業には1日につき1時間程度割かれていましたし、それ以外にも、細菌検査や拭き取り検査などの結果は、チェックシートからExcelに転記してデータ化する作業を行っていました。
こうしたデータは、事故防止や作業の適正化に役立てるために蓄積していましたが、日常の業務に追われて分析まで時間をかけられないというのが実情でした。
そのほか、管理職にとっては、紙のチェックシートへの記入ミスや記入漏れが課題でした。
HACCPの完全義務化に伴い、食品製造の品質管理が厳しくなり、確認が必要な項目は細分化・複雑化しています。しかし、チェックシートの用紙サイズは、後の管理を考慮するとA4サイズが望ましいため、記入する枠や文字を小さくせざるを得ません。そのため、現場の従業員は記入ミスや記入漏れを起こしやすく、特に新入社員の場合、チェックシートの正しい記入方法を覚えるまでに時間がかかるといった状況でした。これでは、記入後のチェックシートを確認する管理職に大きな負担がかかります。
チェックシートの確認は作業終了後に行うため、管理職は作業で疲労した状態で細かい記入項目に目を通さなくてはいけません。そうしたなかで、記入ミスや記入漏れを見つけ出し、従業員に注意・指導を行うのは非常に手間のかかる作業でした。


選定理由
カミナシ導入の決め手は「食品会社での導入実績の多さ」
── カミナシを導入された経緯を教えてください。
飯嶋様:お話したような課題の解決を目指して、作業記録を電子化できるシステムの導入を検討しました。そのなかで、カミナシさんのWEBサイトに辿り着き、食品製造会社での導入実績を多数有しているのを知り、導入を決めました。
── その後、どのように導入を進められましたか。
飯嶋様:私が中心になってテンプレートを作成しました。
私自身、Excelを日常的に使う程度で、プログラミングのスキルは有していませんが、カミナシはノーコードでテンプレートの設定が可能なため、スムーズに導入を進めることができました。また、チャットでカミナシのカスタマーサポートに質問できるため、操作などに悩んだときも、導入が滞るようなケースはほぼありませんでした。
活用状況
カミナシの画像撮影機能を活用して、無駄なラベル発行を効率化
── カミナシの現在の活用状況を教えてください。
飯嶋様:工場にタブレットを10台導入し、約20人の従業員で使用しています。
活用方法としては、まず、無駄なラベルの削減を目的に、ラベル発行時や貼付時の作業記録に使用しています。以前は、ラベルを発行した際にチェックシートに賞味期限などを転記していたのですが、現在はカミナシに所定項目を入力した後に、ラベルの画像を撮影しています。これにより、ラベルの画像がカミナシ上で共有されるため、確認用のラベルを発行する必要がなくなります。
カミナシのアプリで画像を撮影できる機能は非常に便利で、原料肉や調味料などの副資材を受け入れるときのロット管理や、設備機器などの始業終業点検にも活用しています。
また、以前はチェックシートで行っていた健康チェックや検品記録、細菌検査、拭取り検査、落下菌検査などの作業記録はカミナシに移行しました。
そのため、品質管理部門におけるチェックシートの仕分けやファイリングなどの作業は、これまで1時間程度かかっていたものが、現在では10〜15分程度にまで削減できました。
また、細菌検査や拭き取り検査などのデータはカミナシからExcelに自動出力しているため、転記作業も不要となりました。手作業でデータを転記する以上、入力ミスは付き物です。そうしたリスクも防止できているのは嬉しい効果です。
さらに、総務部が担当していた来工者の健康チェックや保管庫の鍵の貸出管理記録など、製造以外の領域にもカミナシを活用しています。


導入効果
年間10,000枚以上の用紙削減、25,000枚以上のラベル削減のほか、作業時間の削減など数々の効果を実現
── カミナシの活用により、どのような効果が生まれていますか。
飯嶋様:まずは、ラベルやチェックシートの用紙削減です。以前、チェックシートには1日で120〜130枚の用紙を費やしていましたが、現在では全体の4割程度を削減できています。
年間に換算すれば10,000枚以上の用紙削減効果です。ラベルに関しては、1日で約80枚程度を削減しており、年間では25,000枚以上の削減効果が出ています。
また、業務負担の軽減効果も現れています。例えば、確認用のラベルを発行しなくなったことにより、製造部の従業員は品質管理部へのラベル発行依頼を省略でき、1日で約20分の業務を削減しました。
一方、品質管理部については、チェックシートの仕分けやファイリング、Excelへのデータ転記作業、ラベルの発行作業など、数々の作業が省略され、1日で約1時間の業務削減効果が生まれました。
私自身、品質管理部のメンバーとして、カミナシの導入による生産性向上を強く実感しています。
さらに、チェックシートでの作業記録時にはしばしば発生していた、記入ミスや記入漏れがほぼゼロにまで減っています。
カミナシのテンプレートは一問一答形式であり、さらに所定項目を入力しないと次の作業に移行できない設定を施せるため、記入漏れを減らすことが可能です。また、従業員が規定から外れた数値や内容を入力した場合には、アラートを表示することもできるため、記入ミスも低減できます。
これにより、管理職による作業記録の確認が大幅に効率化しました。これまでは作業終了後に、チェックシートの項目を一つひとつ確認しなければいけませんでしたが、現在では記入ミスが疑われる項目にはアラートが表示されるため、スムーズに作業記録の確認を終えられています。


今後の展望
今後はカミナシで収集したデータを二次利用し、予兆保全などに役立てたい
── カミナシの活用について、今後の展望をお聞かせください。
飯嶋様:カミナシで蓄積したデータを活用して、データの二次利用を推進していきたいです。例えば、現在、カミナシでは照明器具の照度確認や温度計精度管理、計量器精度管理などの作業記録も行っており、日々、データが蓄積されていっています。こうしたデータを分析し、設備機器の予兆保全などに活用したいと考えています。
作業記録を紙のチェックシートで行った場合、記録を集計してデータ化し、二次利用可能な状態に整えるだけでも多大な時間がかかります。しかし、そうした作業が現在では、ほぼ自動的に行えているのは、まさに一石二鳥です。カミナシの導入により、その他の業務負担も軽減されたことですし、今後は様々なデータを二次利用し、事故防止や従業員の作業の適正化などにも役立てていきたいです。
── 飯嶋様、本日はありがとうございました!


この事例を見た方は
こんな事例も
読んでいます